The seamless construction of
seamless steel gas cylinders offers several significant advantages compared to cylinders with welded seams. These advantages contribute to the cylinders' enhanced safety, performance, and reliability. Here are some key benefits of seamless construction:
Reduced Risk of Weak Points: Welded seams can create potential weak points in a cylinder's structure, making it more susceptible to stress concentration, fatigue, and corrosion. Seamless construction eliminates these seams, providing a more uniform and continuous material structure that minimizes the risk of weak points.
Higher Pressure Capacity: Seamless steel cylinders can withstand higher internal pressures compared to cylinders with welded seams. The absence of welded joints means there are no areas prone to stress concentrations that could limit the cylinder's pressure capacity. This higher pressure capability allows seamless steel cylinders to store gases at greater pressures, making them suitable for a broader range of applications.
Enhanced Safety: Seamless construction contributes to improved safety by reducing the likelihood of sudden failures or leaks due to weak seams. This is especially critical when storing or transporting potentially hazardous gases.
Better Resistance to Corrosion: Welded seams can be more vulnerable to corrosion, as they create areas where moisture and corrosive agents can accumulate. Seamless cylinders are less susceptible to corrosion at welded joints, helping to extend the cylinder's lifespan and maintain its integrity.
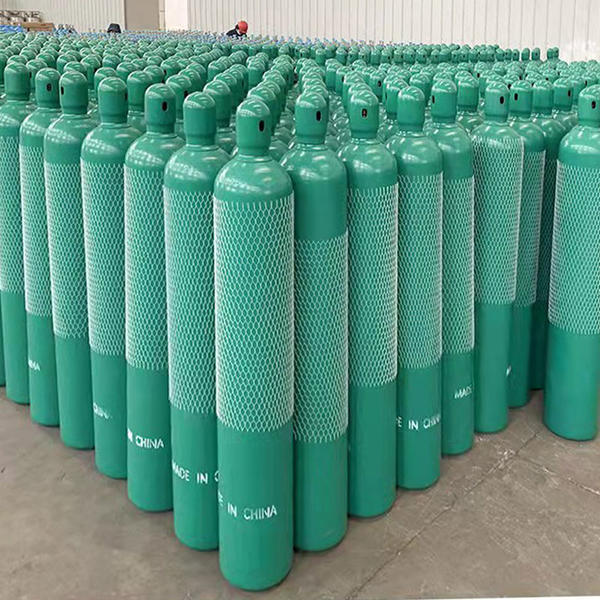
Improved Aesthetics and Hygiene: Seamless construction provides a smoother and cleaner appearance, which is particularly important for cylinders used in medical applications or industries where cleanliness and hygiene are essential.
Consistent Mechanical Properties: Seamless construction results in more consistent mechanical properties throughout the entire cylinder, reducing variations in material strength and performance. This consistency enhances the cylinder's reliability and predictability under varying conditions.
Reduced Maintenance Requirements: The absence of welded seams reduces the need for maintenance and repairs associated with seam integrity. This can lead to lower maintenance costs and downtime.
Easier Inspection: Seamless cylinders are often easier to inspect visually, as there are no seams to scrutinize for signs of stress, corrosion, or fatigue. This can facilitate quicker and more accurate inspections.
Wide Range of Applications: The strength, safety, and high-pressure capacity of seamless steel cylinders make them suitable for a wide range of applications, including industrial gases, medical gases, firefighting, aerospace, and more.
Regulatory Compliance: Many international standards and regulations specify requirements for the design, manufacturing, and use of gas cylinders. Seamless construction helps ensure compliance with these standards, contributing to the overall safety and quality of the cylinders.
The seamless construction of seamless steel gas cylinders provides multiple benefits that contribute to their superior performance, safety, and reliability in storing and transporting compressed gases. These advantages make seamless steel cylinders a preferred choice in various industries where pressure vessels are required.