Cryogenic liquid pumps are at the forefront of various industries, propelling the boundaries of science and technology. However, the specter of cavitation looms over these pumps, posing a significant challenge. Understanding how to prevent cavitation in cryogenic liquid pumps is crucial for ensuring their optimal performance and longevity. Let’s explore the intricacies of cavitation in this context and unravel the measures to mitigate its impact.
Cavitation, the formation and subsequent collapse of vapor bubbles within a liquid, can wreak havoc on
cryogenic liquid pump. The extreme temperature conditions at which these pumps operate make them particularly susceptible to cavitation. The rapid changes in pressure and temperature can lead to the formation of vapor pockets within the pump, causing erosion, noise, and reduced efficiency. To combat this phenomenon, engineers have devised innovative solutions such as optimizing the pump’s inlet design, increasing the net positive suction head (NPSH), and employing advanced materials to mitigate the effects of cavitation.
Preventing cavitation in cryogenic liquid pumps is of paramount importance due to the critical nature of the applications in which these pumps are utilized. For instance, in the context of space exploration, the reliability and efficiency of cryogenic pumps directly impact the success of missions. Cavitation-induced damage can compromise the performance of these pumps, jeopardizing the delivery of cryogenic propellants essential for launching rockets. Similarly, in medical applications such as MRI machines, the presence of cavitation can lead to operational disruptions and compromise the quality of medical imaging, underscoring the significance of mitigating cavitation in cryogenic liquid pumps.
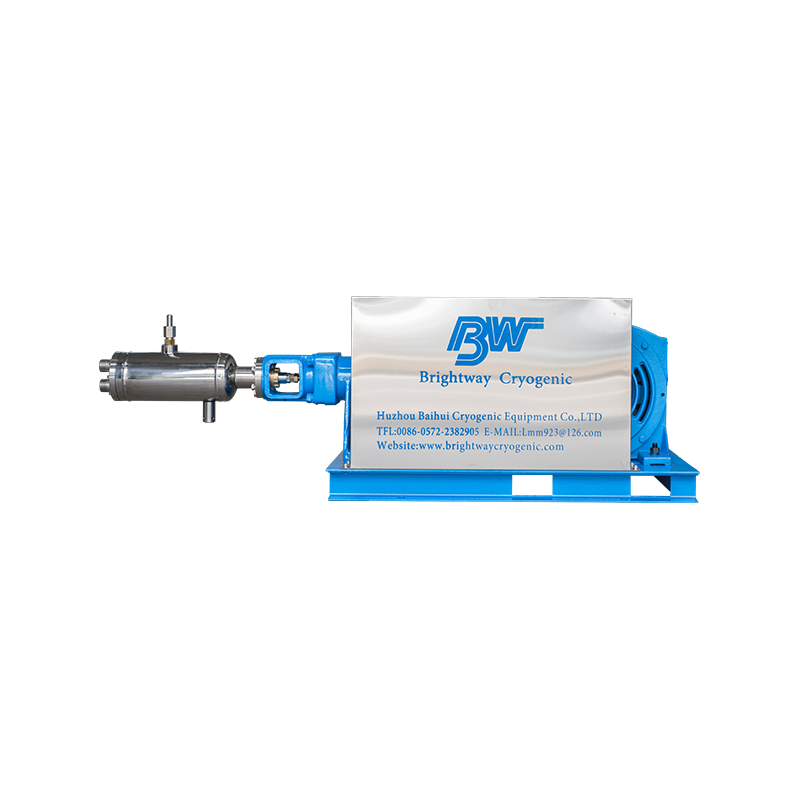
The prevention of cavitation in cryogenic liquid pumps is pivotal in the realm of renewable energy, where these pumps play a crucial role in superconducting power transmission. Cavitation-induced erosion can compromise the integrity of the pump components, leading to costly maintenance and downtime. By implementing effective cavitation prevention measures, such as optimizing the pump’s hydraulic design and employing advanced computational fluid dynamics (CFD) simulations, the reliability and longevity of cryogenic pumps can be significantly enhanced, ensuring seamless operation in the burgeoning field of clean energy infrastructure.
The prevention of cavitation in cryogenic liquid pumps is a multifaceted endeavor with far-reaching implications across industries. The relentless pursuit of innovative solutions to mitigate cavitation is pivotal for safeguarding the performance and reliability of cryogenic pumps in critical applications such as space exploration, medical technology, and renewable energy. As the demand for efficient and resilient cryogenic pumping systems continues to grow, the ongoing advancements in cavitation prevention techniques will play a pivotal role in shaping the future of this indispensable technology.